Cleanroom and cleanliness technology is essential for industries requiring strict sterility and particle control. This text explores key aspects of planning and maintaining effective cleanroom solutions.
Reading time: 4 minutes
Comprehensive Planning and Implementation
Cleanroom and cleanliness technology is crucial for maintaining optimal conditions in industries that demand the highest levels of sterility and particle control. From pharmaceuticals to electronics, ensuring a controlled environment is essential for product quality and compliance with international standards. This text delves into the core aspects of planning, implementing, and maintaining cleanroom solutions to enhance efficiency and meet rigorous standards.
The development of efficient cleanrooms begins with meticulous planning that considers industry-specific requirements. Factors such as air quality, pressure differentials, and temperature regulation play a pivotal role in ensuring the desired cleanliness levels. Proper material selection is essential—antimicrobial coatings and seamless surfaces can minimize contamination risks.
Integrating Building Information Modeling (BIM) into the design phase allows all stakeholders to collaborate effectively, optimizing space utilization and streamlining workflows. BIM's detailed visualization aids in preventing potential design conflicts and supports precise material calculation, ensuring sustainability and cost-efficiency.
Core Considerations in Planning:
- Air Filtration: Incorporation of HEPA and ULPA filters for high-level particle control.
- Material Selection: Use of non-porous, easy-to-clean materials that support hygiene.
- Temperature and Humidity Control: Systems to maintain stability within critical ranges.
Advanced Cleanroom Systems and Technologies
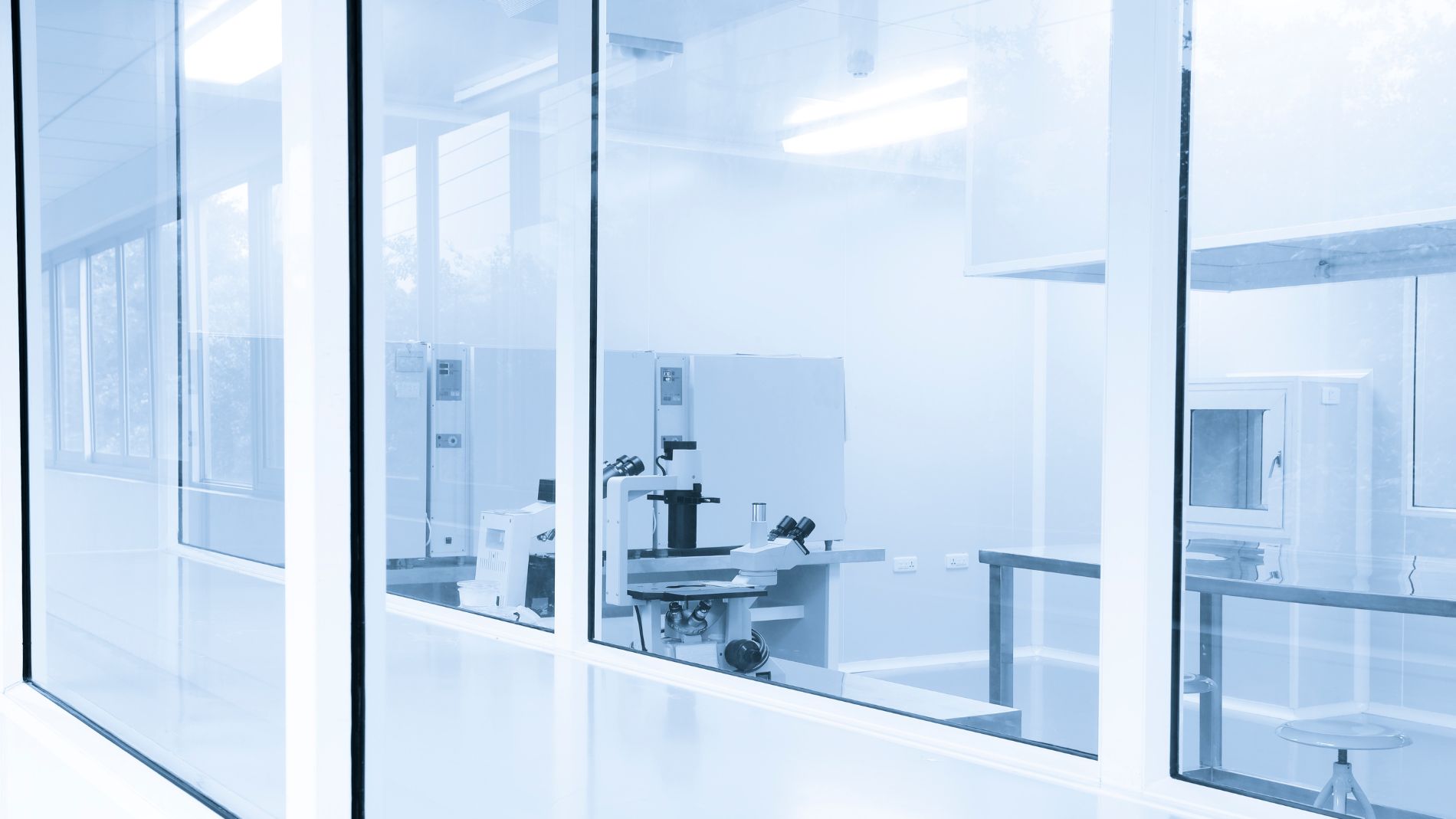
Modern cleanroom solutions leverage state-of-the-art technologies to maintain stringent cleanliness levels. IoT-enabled sensors provide real-time data on air quality and system performance, allowing for immediate adjustments to maintain compliance. Automation systems can manage airflow, filtration, and temperature regulation, reducing manual intervention and enhancing operational efficiency.
The integration of smart monitoring technology also supports predictive maintenance, identifying issues before they escalate into costly disruptions. This proactive approach extends the life of equipment and sustains a consistent production environment.
Sustainable Practices and Efficient Maintenance
Sustainability in cleanroom operations focuses on reducing energy consumption and maintaining effective cleanliness without excessive resource use. Advanced HVAC systems with energy recovery capabilities help to minimize power usage while ensuring continuous air purification. Regular maintenance routines, combined with automated cleaning technologies, maintain high cleanliness standards and extend the life cycle of cleanroom components.
Hygiene Protocols and Continuous Validation
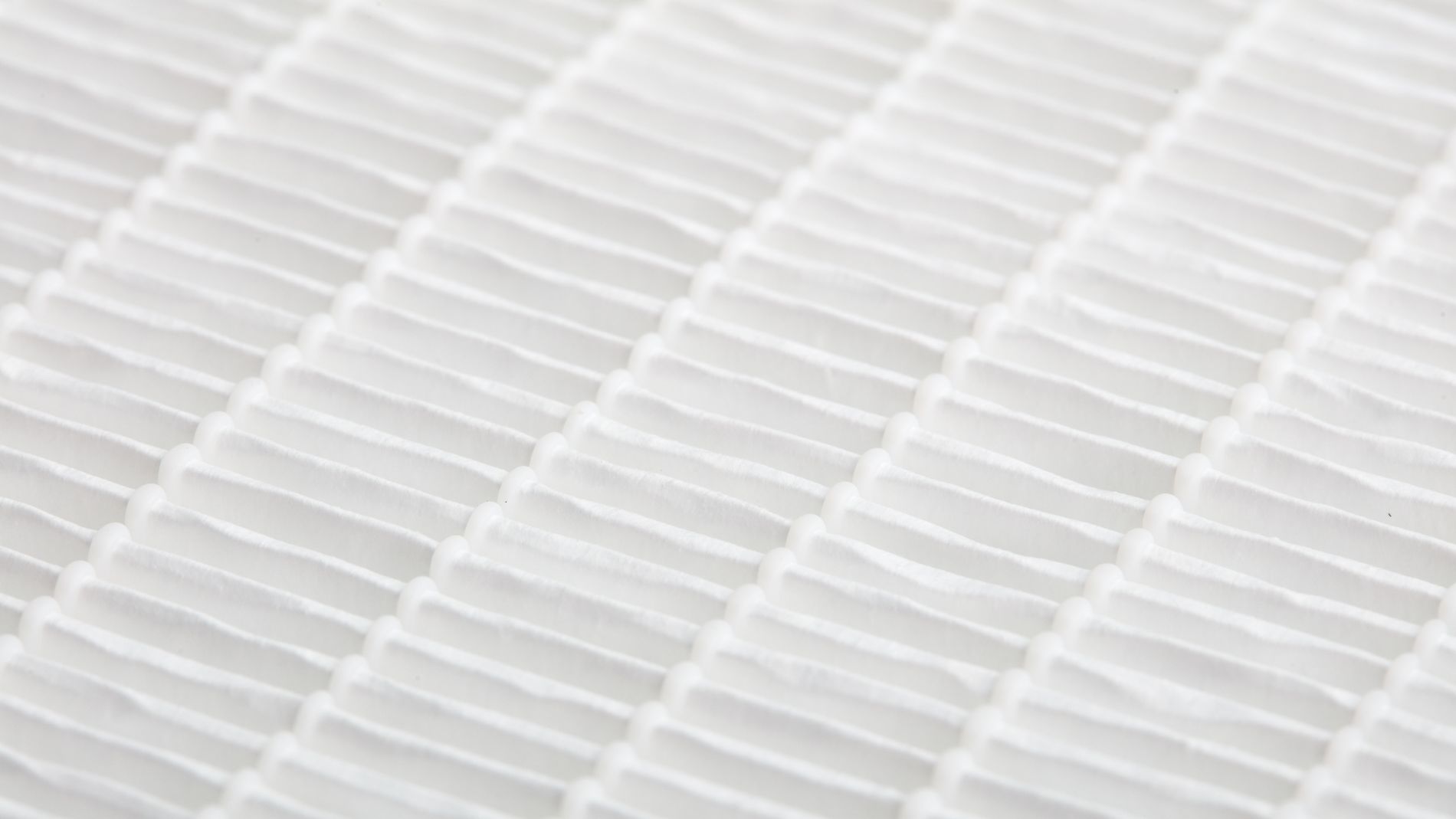
Routine validation processes are essential to verify that cleanrooms meet global industry standards. Cleanroom validation includes air quality tests, particle counts, and airflow analysis to ensure performance remains optimal. The use of digital tools for continuous monitoring supports compliance and minimizes the risk of human error, maintaining a sterile environment conducive to high-quality production.
FAQ
What are the key factors to consider when planning a cleanroom?
Key considerations for planning a cleanroom include selecting appropriate materials, ensuring effective air filtration with HEPA or ULPA filters, and maintaining temperature and humidity controls. Incorporating technologies such as BIM can streamline the planning process, allowing for precise visualization and minimizing design conflicts.
How can cleanroom energy efficiency be improved?
Energy efficiency in cleanrooms can be enhanced by using advanced HVAC systems with energy recovery capabilities, integrating IoT sensors for real-time monitoring, and implementing automated airflow management. Sustainable practices such as periodic maintenance and the use of energy-efficient lighting also contribute to overall energy savings.
What role does predictive maintenance play in cleanroom operations?
Predictive maintenance involves using smart monitoring systems to detect potential issues before they escalate. This approach helps maintain equipment performance, reduces downtime, and prolongs the life of cleanroom infrastructure by addressing maintenance needs proactively, ensuring continuous operation and compliance with cleanliness standards.